Aluminum Spreading Solutions Unveiled: Important Insights and Tips
Exploring the world of aluminum spreading services can introduce a world of intricate procedures and nuanced considerations that are essential for effective end results. As industries significantly turn to aluminum for its light-weight yet long lasting residential or commercial properties, recognizing the fundamentals of casting ends up being paramount. From the essential strategies to the elaborate information that can make or damage a casting job, there is a wide range of insights and ideas waiting to be discovered. So, as we venture right into the world of light weight aluminum spreading services, prepare to reveal the essential elements that can form the trajectory of your tasks and elevate your understanding of this elaborate craft.
The Essentials of Light Weight Aluminum Spreading
What fundamental procedures are entailed in light weight aluminum casting that form the foundation of this commonly used manufacturing strategy? Aluminum casting is a functional and affordable technique utilized in various industries to produce complicated and elaborate steel elements.
Key elements such as mold layout, gating system, and cooling price play a critical duty in figuring out the final top quality of the cast light weight aluminum part. The mold can be constructed from different products like steel, sand, or financial investment spreading wax, depending on the intricacy of the component and the desired surface coating. After solidification, the mold is gotten rid of, and the spreading undertakes completing processes such as heat therapy, surface, and machining finishing to fulfill the needed specs. Recognizing these essential processes is vital for accomplishing high-grade light weight aluminum castings with specific dimensions and mechanical properties.
Various Casting Approaches Explained
Checking out the numerous techniques utilized in light weight aluminum casting uses important insights into the varied approaches made use of to achieve detailed and exact steel elements. One common approach is sand spreading, where a mold is produced utilizing compressed sand around a pattern of the desired part. One more approach, pass away spreading, involves injecting molten light weight aluminum right into a steel mold and mildew under high stress.
Factors to Think About When Selecting a Service Provider
When choosing an aluminum spreading company, evaluating their experience and know-how is critical for ensuring quality and dependability in the manufacturing process. The supplier's experience in the area shows their knowledge with various spreading strategies, possible obstacles, and ideal techniques. It is crucial to make inquiries concerning the kinds of tasks they have actually worked with in the past, ensuring they align with the complexity and specs of your own project.
In addition, take into consideration the carrier's track record within the market. Look for testimonials, testimonials, and study that demonstrate their ability to supply top quality aluminum spreadings constantly. A trusted carrier will frequently have qualifications or affiliations with industry organizations, showcasing their dedication to quality and adherence to market requirements.
Furthermore, assess the service provider's capacities in terms of modification, volume demands, and task timelines. Make sure that they can accommodate your certain needs and have the versatility to scale manufacturing as required. Reliable interaction and transparency pertaining to prices, lead times, and top quality control processes are likewise critical factors to take into consideration when choosing an aluminum spreading service carrier.
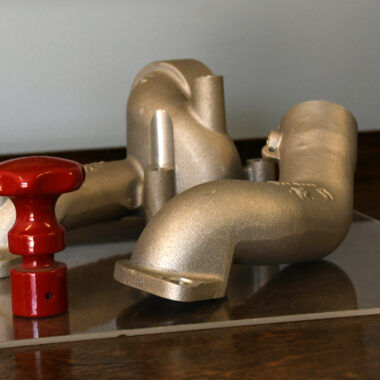
Usual Obstacles and Solutions
Navigating with the intricacies of light weight aluminum casting procedures often provides manufacturers with a series of difficulties that call for ingenious remedies to ensure effectiveness and quality in manufacturing. One common difficulty encountered in aluminum casting is the development of problems such as porosity, shrinking, or incorporations due to improper mold layout or inadequate steel top quality.
Another difficulty exists in attaining exact dimensional precision, especially for complex geometries. Variations in cooling down prices, mold growth, and product properties can result in variances from the designated dimensions. Implementing sophisticated innovations like computer-aided layout (CAD) and computer system mathematical control (CNC) machining can boost precision and consistency in aluminum spreading. Furthermore, preserving appropriate control over the melting and putting procedures is critical to stop issues like overheating or unequal circulation of the molten metal - casting aluminum. By investing in automation and real-time surveillance systems, manufacturers can boost procedure control and lessen variants, inevitably boosting the general high quality of aluminum cast products.
Tips for Optimizing Your Spreading Projects
To boost the performance and top quality of your aluminum casting have a peek at this website projects, applying critical optimization methods is vital. One crucial suggestion for optimizing your spreading projects is to carefully make eviction system. By guaranteeing that the gating system is properly designed and correctly positioned, you can boost the circulation of molten light weight aluminum and reduce the opportunities of issues in the final spreading. Furthermore, utilizing computer system simulations can help in forecasting and examining the flow of steel during the spreading process, permitting modifications to be made prior to actual manufacturing begins.

Verdict
In conclusion, recognizing the fundamentals of light weight aluminum spreading, different casting approaches, variables to take into advice consideration when choosing a carrier, common difficulties and remedies, and ideas for maximizing casting tasks are vital for effective end results. By adhering to these understandings and executing finest practices, individuals and services can guarantee effective and efficient aluminum spreading solutions that fulfill their specific needs and requirements.
Comprehending these essential processes is vital for accomplishing top notch light weight aluminum spreadings with specific measurements and mechanical properties.
When picking an aluminum spreading solution provider, examining their experience and knowledge is critical for guaranteeing high quality and dependability in the manufacturing process. Effective interaction and openness relating to expenses, lead times, and high quality control processes are additionally vital elements to think about when choosing a light weight aluminum spreading service carrier.
Browsing with the complexities of light weight aluminum casting procedures commonly provides manufacturers with a collection of difficulties that require cutting-edge services to ensure effectiveness and top quality in production. One usual difficulty encountered in aluminum spreading is the formation of defects such as porosity, shrinking, Read Full Report or inclusions due to incorrect mold design or insufficient steel high quality.